Enhancing Workforce Management With FOYCOM RFID Cloud
This case study highlights how FOYCOM helped HVAC machinery manufacturers with advanced attendance management, real-time production data, compliance, and safety data. Learn more about how they benefited from using the FOYCOM RFID cloud solution.
About HVAC Machinery Manufacturer
In the competitive world of HVAC machinery manufacturing, where precision engineering and worker safety are critical, a leading US-based HVAC equipment producer faced mounting operational challenges. With facilities spanning 500,000 sq. ft. in Ohio and Texas, the company supplies commercial and industrial HVAC units worldwide. However, legacy workforce management systems hindered their ability to track 1,200+ employees across complex assembly lines, testing zones, and hazardous machinery areas. Manual attendance logs, inefficient floor monitoring, and compliance risks threatened productivity and safety in an industry where strict OSHA standards and on-time delivery are non-negotiable. Partnering with FOYCOM, they deployed an RFID Cloud solution to transform boots into smart sensors—turning workforce visibility from a bottleneck into a strategic advantage. This case study explores how a global manufacturing leader revolutionizes workforce management, achieving measurable gains in productivity, compliance, and data-driven decision-making.
Challenges Faced By HVAC Machinery Manufacturer
The company faced several challenges that prompted them to explore advanced tracking solutions.
Manual Attendance Records
Traditional methods of recording employee entry and exit were error-prone and time-consuming.
Limited Visibility on Floor Time
The lack of real-time data on time spent by workers in specific zones impacted productivity analysis.
Compliance & Safety Concerns
Monitoring movement in restricted areas was essential to ensure safety and compliance with workplace regulations.
Scalability Issues
Existing systems struggled to accommodate a growing workforce and complex workflows.
Get FREE Consultation
Solution From FOYCOM
FOYCOM introduced an innovative RFID Cloud solution to address these challenges. The system leverages RFID tags embedded in the soles of worker boots, combined with strategically placed RFID readers throughout the facility.
Key features of the solution include:
Automated Entry/Exit Tracking
RFID readers at entry and exit points automatically log worker movement.
Time-on-Floor Analysis
Real-time data collection on the duration workers spend in specific zones.
Integration with ERP Systems
Seamless synchronization with existing ERP systems for centralized reporting.
Customizable Alerts
Notifications for unauthorized access to restricted areas or unusual activity patterns.
Features & Benefits of FOYCOM RFID Cloud
Here we have listed key features with which the client benefited from using the FOYCOM RFID Cloud solution.
Implementation Process
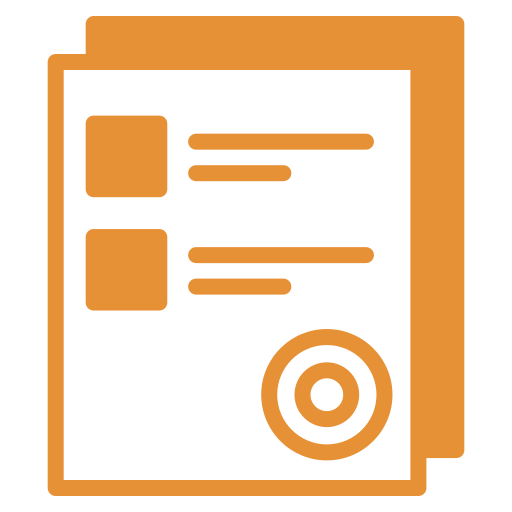
Assessment & Planning
FOYCOM conducted a thorough analysis of the production floor layout and workflows.
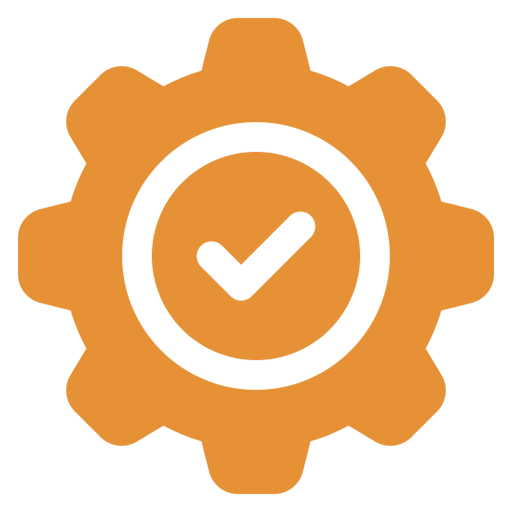
Hardware Installation
RFID readers were installed at strategic locations, including entrances, exits, and critical zones.
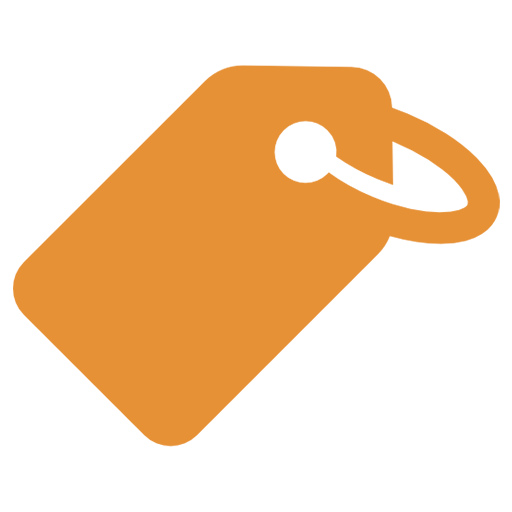
Boot Tagging
All worker boots were equipped with durable RFID tags resistant to industrial conditions.
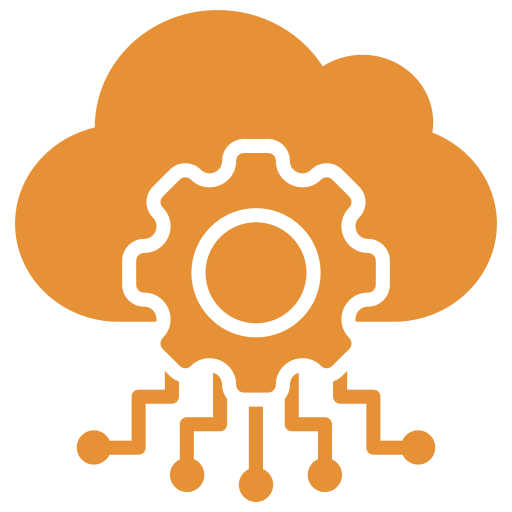
Cloud Integration
The RFID system was connected to the FOYCOM Cloud platform for real-time data collection and analysis.
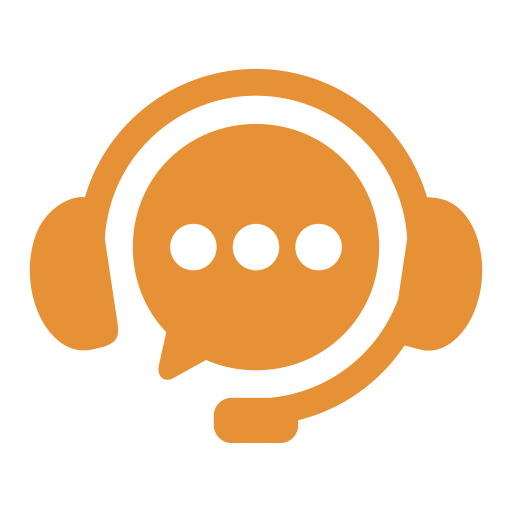
Training & Support
Employees were trained to understand the system, and a dedicated support team was deployed for ongoing assistance.
Revolutionize Workforce Efficiency with FOYCOM RFID Cloud
Automate tracking, improve compliance, and unlock actionable insights for a smarter, safer workplace.
Results & Benefits
The implementation of the FOYCOM RFID Cloud system delivered remarkable improvements:
Increased Efficiency
Automated tracking eliminated manual record-keeping, saving significant time and resources.
Enhanced Productivity
Real-time data allowed supervisors to optimize workforce allocation and identify bottlenecks.
Improved Safety & Compliance
The system ensured that only authorized personnel accessed restricted areas.
Actionable Insights
Detailed analytics provided insights into employee attendance, zone activity, and overall productivity.
Scalability
The solution easily scaled to accommodate the company's growing workforce and future expansion plans.
Conclusion
FOYCOM's RFID Cloud solution redefined workforce management for the manufacturer, proving that innovation can harmonize efficiency, safety, and scalability. By automating time tracking, enhancing floor visibility, and enforcing compliance, the company reduced operational costs, mitigated risks, and empowered data-driven leadership. As manufacturing evolves, RFID-driven systems like FOYCOM will remain indispensable tools for companies striving to thrive in Industry 4.0.
Future-ready Smart Manufacturing Starts Here
Partner with FOYCOM to run your manufacturing units using smart data & actionable insights!